This software converts multiple small lines forming arcs in a dxf file into arcs to reduce its size. This enables easy use for CNC projects, and faster completion by the CNC machine.
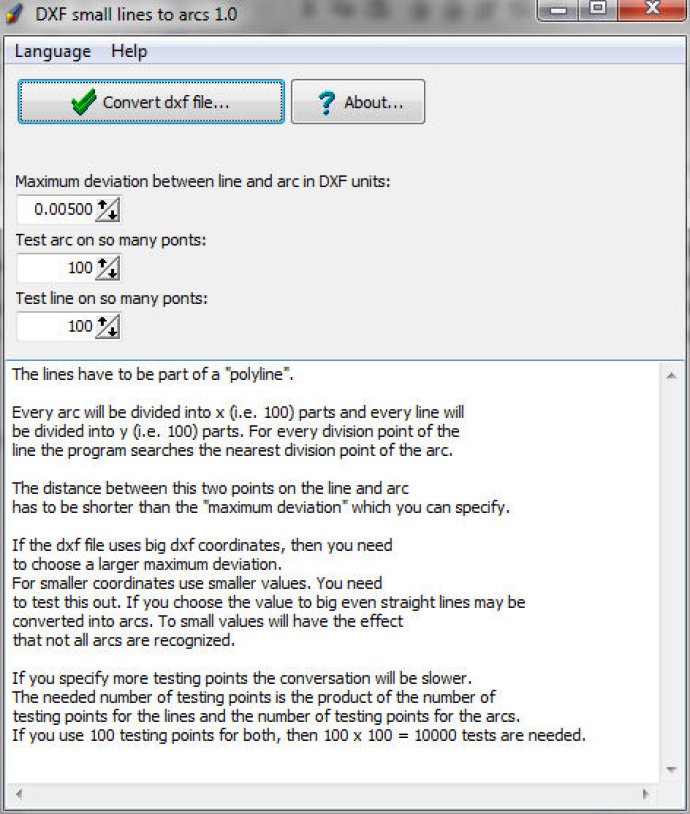
To utilize the software effectively, the lines in the dxf file must be part of a "polyline". Each arc is divided into x (i.e. 100) parts, and each line is divided into y (i.e. 100) parts. The program then searches for the nearest division point of the arc for every division point of the line. The distance between these two points on the line and arc must be shorter than the "maximum deviation" specified by the user.
It is essential to choose the correct "maximum deviation" value, depending on the size of the dxf coordinates used. Larger coordinates require a larger maximum deviation, whereas smaller coordinates require smaller values. This value must be tested thoroughly, as choosing a value that is too big may convert straight lines into arcs, and choosing a value that is too small may result in not recognizing all the arcs.
Moreover, the more testing points specified, the slower the conversion process will be. The number of testing points required is the product of the number of testing points for the lines and the number of testing points for the arcs. For example, if 100 testing points are used for both lines and arcs, then a total of 100 x 100 = 10000 tests are needed.
In conclusion, this software provides a quick and efficient way to convert lines into arcs, which is essential for CNC projects. With careful consideration of the maximum deviation value and the number of testing points, this software can be a valuable asset in any workshop.
Version 1.0: First release